This application note describes a wind turbine gearbox fault test system developed by a client in the industrial automation industry. This customer specializes in Industrial Internet of Things (IIoT) platform design, edge computing system architecture, and industrial-level hardware platform design.
The customer required a testing solution for wind turbines specifically focusing on gearbox diagnostics.
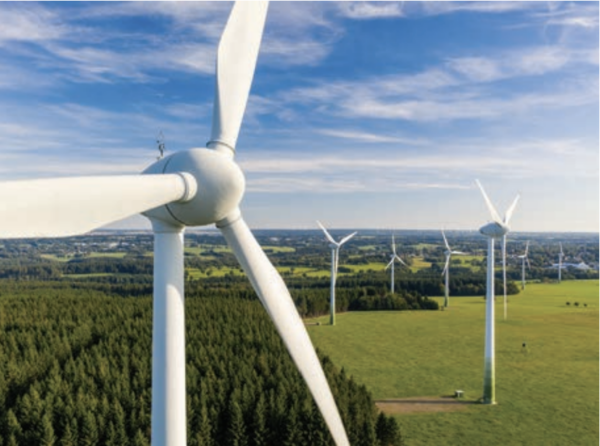
The Challenge
The drivetrain, containing the generator and gearbox, is critical for wind turbine operation. These gearboxes endure harsh conditions that can lead to component failures. While turbines rotate at a slow speed (10-18 RPM), the generator reaches much higher speeds (over 1000 RPM). These contrasting speeds create significant forces on gearbox components. Due to the remote location of wind turbines, gearbox reliability is paramount.
The required test system simulates common bearing failure conditions. By mimicking various operating and load scenarios, the system can identify potential bearing and gear failures before they occur. The customer needed a vibration measurement and analysis solution that was not only functional but also adaptable to their specific needs. The solution would be used in two modes:
- Stand-alone mode: Collect data as part of a test bench, simulating different operating conditions.
- IIoT mode: Deploy the DAQ solution alongside the turbine for real-time data logging and analysis.
The Solution
The WebDAQ 504 was chosen for data acquisition. Two IEPE-based accelerometers connect directly to the WebDAQ, eliminating the need for additional signal conditioning. These channels are sampled simultaneously using the built-in anti-aliasing filtering functions. The horizontal and vertical accelerometers, pre-installed on the gearbox bearings, are sampled at up to 25 kS/sec per channel.
The WebDAQ 504 features a user-friendly web browser interface for setting up data acquisition, logging and displaying data, enabling alarms, and exporting data to third-party applications. In this case, the customer required additional functionality, so direct programming of the WebDAQ was preferred, rather than simply using the browser interface or the REST API.
The WebDAQ 504 utilizes a Raspberry Pi® Compute module as its computing engine. By leveraging the WebDAQ open-source code, programmers were able to directly access the Raspberry Pi, transforming the system into a true edge computing solution. The included Python example programs expedited application development and interfacing with the custom displays and analysis portion of the program.
Operation
- Stand-alone mode: Data is collected from the test bench setup. Vibration data is analyzed in real-time under various operating conditions (load and speed).
- IIoT mode: The WebDAQ 504 is deployed with the turbine, communicating via Ethernet. The system allows connection to the public/private cloud. Through a custom interface, applications like device management, remote monitoring, and health assessment can be implemented for distributed online monitoring and health management scenarios. Additionally, data can be uploaded using the MQTT protocol for integration with secondary data applications.
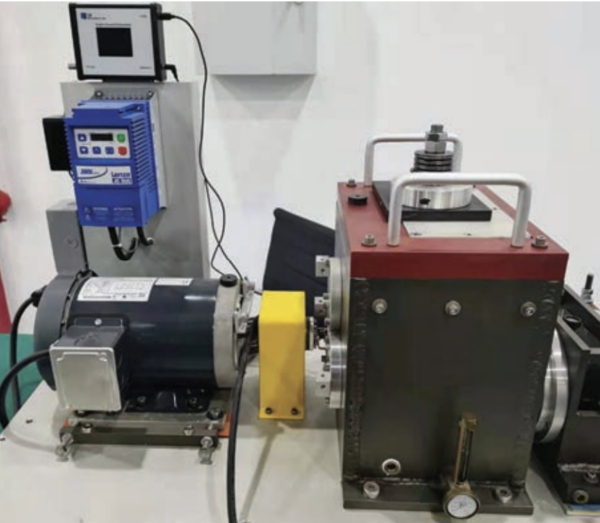
Result
The completed system is a versatile platform for collecting and analyzing vibration data. This vibration analysis application can be used in other similar industrial applications that use pumps, motors, and transportation systems. It fulfills the customer’s specific software needs and has demonstrably enhanced both reliability and reduced maintenance time.